

Liquefied Gas Transfer
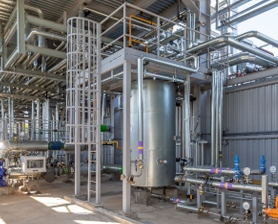
(Click image to enlarge)
We were hired by two leading chemical and industrial gas companies to develop solutions for their liquefied gas transfer processes. One of the clients was a North American company that has served a wide range of major industries for over 75 years and currently has over 15,000 employees operating in 50 countries.
The other client is a Chinese firm whose parent company has worked in the chemical industry for over 60 years. Their chemical processing plant produces over 500 tons of chlorine and 1000 tons of hydrogen chloride annually.
Our Chinese client found Michaels Enterprises Inc. through an industry leading product sourcing and supplier discovery firm, while our North American client heard about our services via word of mouth from numerous engineers and industry experts. Both clients sought a unique solution that would increase the efficiency of transferring liquid ammonia gas from various sized storage vessels to mobile supply tanks.
The Problem
As liquid gas is pumped from a storage tank, the gas boils as it releases vapor that fills the tank. Since boiling requires heat energy, heat is drawn from the liquid, thereby causing the temperature of the liquid gas to drop. This decrease in temperature reduces the flow rate and overall pressure in the storage tank and increases the differential pressure across the pump, significantly slowing down the gas transfer delivery process.
To solve this problem, an external heat source is needed to heat the liquefied gas and maintain a consistent pressure between the supply vessel and the storage vessel. Once the differential pressure is reduced, a constant gas transfer rate can be maintained.
The Process and Solution
Our clients needed a custom-made silicone rubber heater that could supply heat back to the liquefied gas effectively. To ensure that we clearly understood their project requirements, we worked together with them at every stage to develop the best possible solution.
The design process started with the engineers from both firms communicating directly with our engineering department. This engineer-to-engineer communication from both ends was necessary to ensure that the scope and technical requirements of the projects were clearly defined from the project's inception.
The initial design drawings and specifications were then continuously revised and updated by our engineering team until it reflected the most feasible option. In one particular case, the client frequently requested revisions to the power and voltage requirements, which we had to take into account when designing and manufacturing the actual product.
One of the main challenges faced by our team was designing a custom heater suitable for use in Class 1 hazardous locations as defined by the NFPA 70® - National Electrical Code® (NEC) and the Canadian Electrical Code (CEC). Class 1 locations are areas that contain flammable gases or vapors in sufficient quantities to pose a risk of explosion or ignition. Michaels Enterprises' heaters are not approved or certified by any agency for a Class 1 Division 2 environment, but we can create heaters suitable for such environments.
Since the silicone heaters were meant to operate in an environment exposed to copious amounts of gas vapors, specific electrical grounding mechanisms had to be put in place to prevent electrical arcing and eliminate sources of potential ignition.
The Results
With the project scope and technical requirements finalized, our engineering department began the research and development (R&D) and manufacturing processes. Several prototypes were subjected to our rigorous quality control and quality assurance procedures to ensure that the product met the clients' specifications, as well as the stringent standards set by the NEC for equipment in Class I environments.
The final solution consisted of multiple silicone rubber heaters working in tandem to limit temperature losses during the liquid gas transfer process. For bigger vessels (the largest one being about the size of a train car), more than a dozen silicone rubber heaters were utilized. Ultimately, the projects were a resounding success. Heat was evenly distributed to the supply tank, and consistent liquid-gas flow rates were achieved, saving the clients time, money, and manpower. Regular and effective communication between our engineers and our clients played a significant part in the project's overall success.
Although these projects presented challenges for our engineering and design teams, they both stood as a testament to Michaels Enterprises Inc's ability to design and manufacture products that meet the strictest environmental and safety specifications.
To learn more about our custom designed silicone rubber heaters and how they can benefit your project, contact us today to request a quote.